SERVICES & PROCESSES
quality
We achieve quality through processes such as our Business Operating System (BOS) where all policies, procedures, instructions, and forms are maintained; a lessons learned database; and integrated quality in station methodology.
SERVICES & PROCESSES
quality
We achieve quality through processes such as our Business Operating System (BOS) where all policies, procedures, instructions, and forms are maintained; a lessons learned database; and integrated quality in station methodology.
LESSONS LEARNED
database
The Dakkota Lessons Learned Database is reviewed annually by corporate quality. Lessons are sorted and prioritized by process for top issues. Then we collaborate with team members of affected areas to improve procedures, followed by training.
LESSONS LEARNED
database
The Dakkota Lessons Learned Database is reviewed annually by corporate quality. Lessons are sorted and prioritized by process for top issues. Then we collaborate with team members of affected areas to improve procedures, followed by training.
LESSONS LEARNED
database
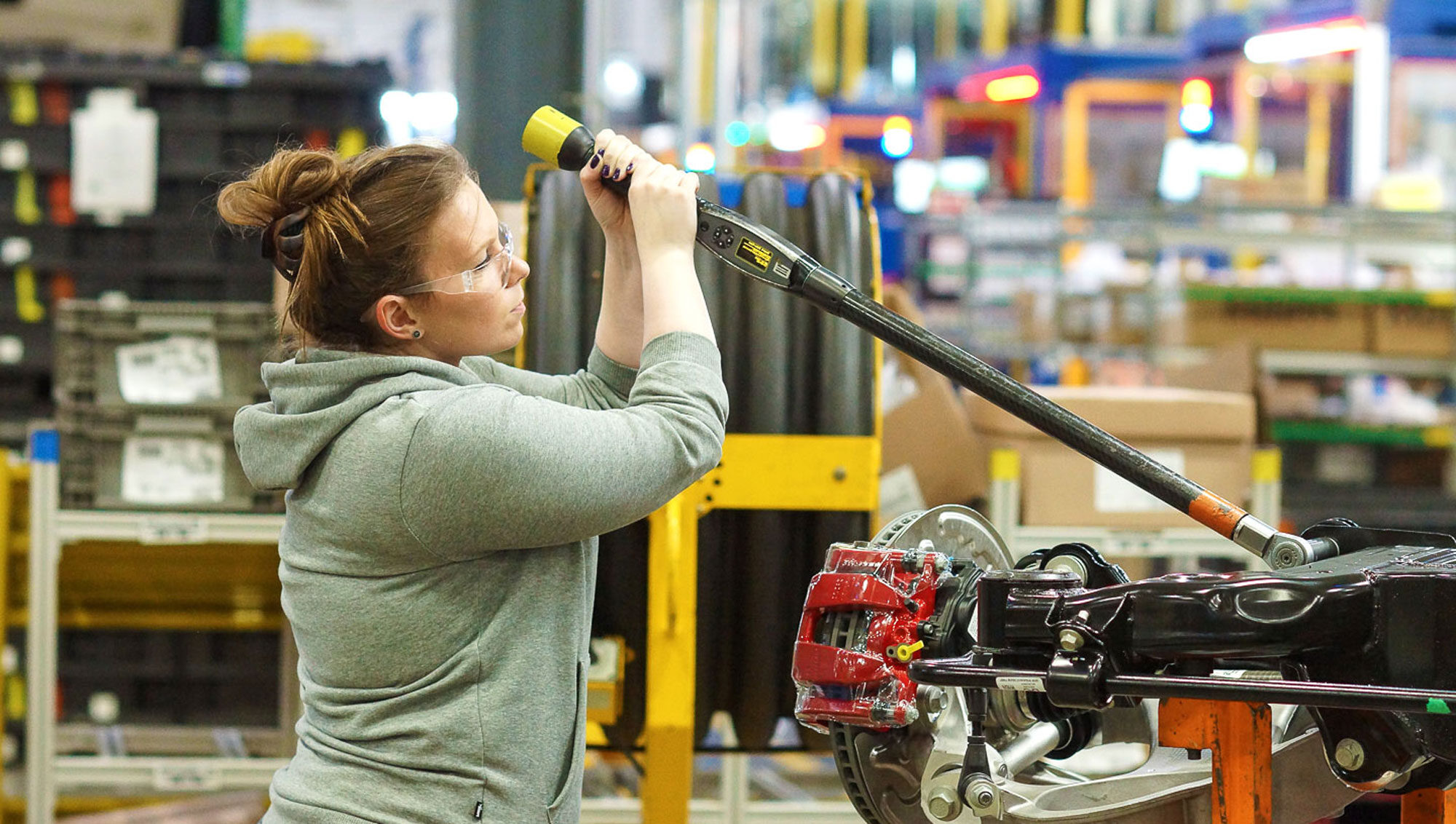
The Dakkota Lessons Learned Database is reviewed annually by corporate quality. Lessons are sorted and prioritized by process for top issues. Then we collaborate with team members of affected areas to improve procedures, followed by training.
BOS
annual review
Our Business Operating System (BOS) is where all policies, procedures, instructions, and forms are maintained. BOS defines how we operate with consistency across all plants. Training plans are generated for all sites and processes are prioritized for each functional area. We require an annual review of all procedures by process owners for accuracy, adaptability of lessons learned, and improvements.
BOS
annual review
Our Business Operating System (BOS) is where all policies, procedures, instructions, and forms are maintained. BOS defines how we operate with consistency across all plants. Training plans are generated for all sites and processes are prioritized for each functional area. We require an annual review of all procedures by process owners for accuracy, adaptability of lessons learned, and improvements.
BOS
annual review
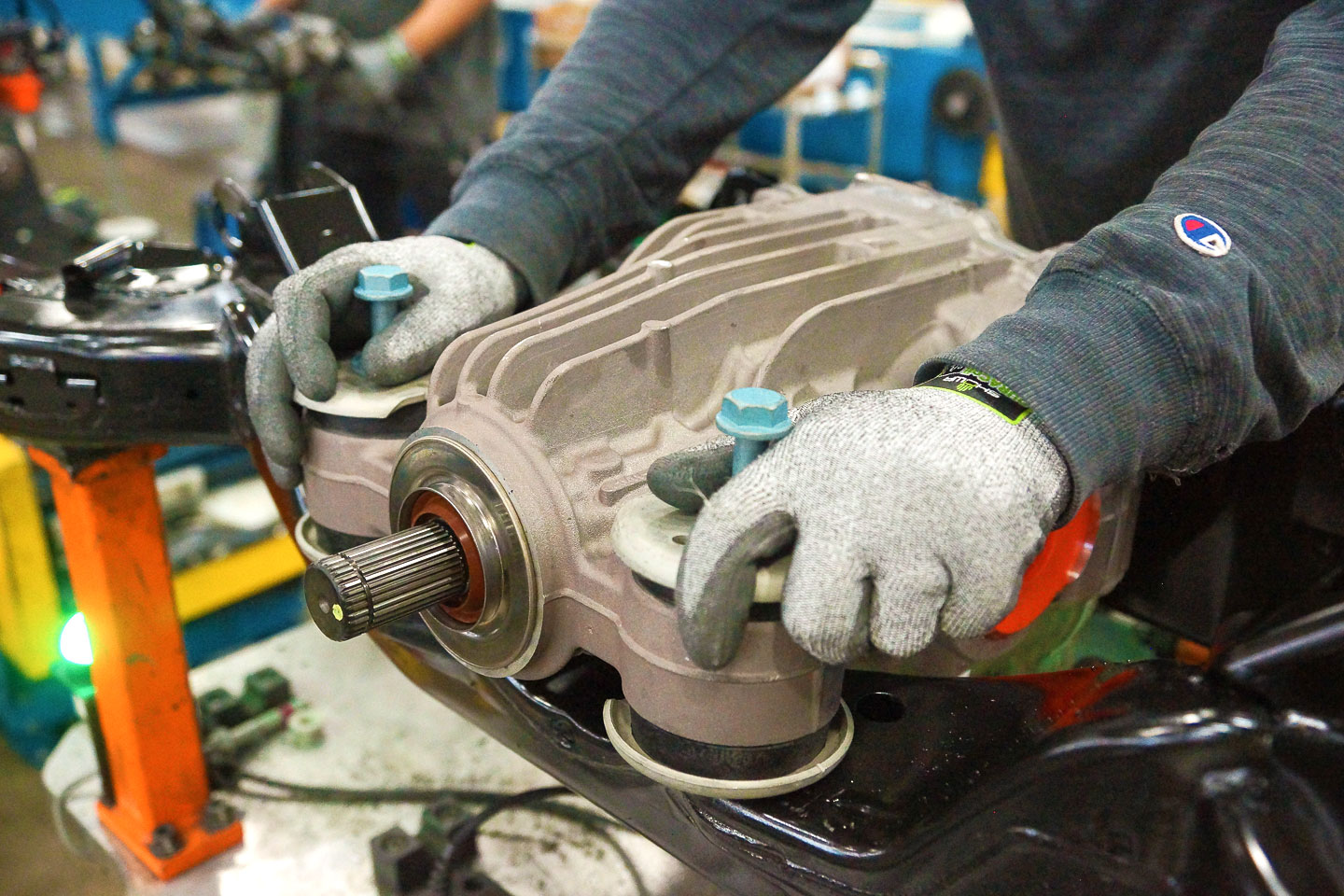
Our Business Operating System (BOS) is where all policies, procedures, instructions, and forms are maintained. BOS defines how we operate with consistency across all plants. Training plans are generated for all sites and processes are prioritized for each functional area. We require an annual review of all procedures by process owners for accuracy, adaptability of lessons learned, and improvements.
ANDON
quality in station
Dakkota team members are trained to inspect product for gross and obvious defects and key quality characteristics. Inspection criteria is part of standardized work for self-confirmation of quality as determined by product and process needs. Andon functionality is integrated into lines and processes to ensure defective product does not move forward.
ANDON
quality in station
Dakkota team members are trained to inspect product for gross and obvious defects and key quality characteristics. Inspection criteria is part of standardized work for self-confirmation of quality as determined by product and process needs. Andon functionality is integrated into lines and processes to ensure defective product does not move forward.
ANDON
quality in station
Dakkota team members are trained to inspect product for gross and obvious defects and key quality characteristics. Inspection criteria is part of standardized work for self-confirmation of quality as determined by product and process needs. Andon functionality is integrated into lines and processes to ensure defective product does not move forward.