SERVICES & PROCESSES
continuous improvement
We’ve been doing what we do for a long time in one of the most intense and demanding industries. Our commitment to quality is driven by an engine of continuous improvement where we are constantly learning how to do what we do better, employ new technology, and listen hard to people on the line who know what it takes.
SERVICES & PROCESSES
continuous improvement
We’ve been doing what we do for a long time in one of the most intense and demanding industries. Our commitment to quality is driven by an engine of continuous improvement where we are constantly learning how to do what we do better, employ new technology, and listen hard to people on the line who know what it takes.
SERVICES & PROCESSES
continuous improvement
We’ve been doing what we do for a long time in one of the most intense and demanding industries. Our commitment to quality is driven by an engine of continuous improvement where we are constantly learning how to do what we do better, employ new technology, and listen hard to people on the line who know what it takes.
QUALITY
circles
Our company-wide quality circles are a key part of Dakkota and are used to improve morale and teamwork through team activity; increase self-development and communication; increase team problem-solving skills; and improve quality, safety, productivity, and the work environment.
We base our quality circle on the six steps in the Plan-Do-Check-Act (PDCA) cycle.
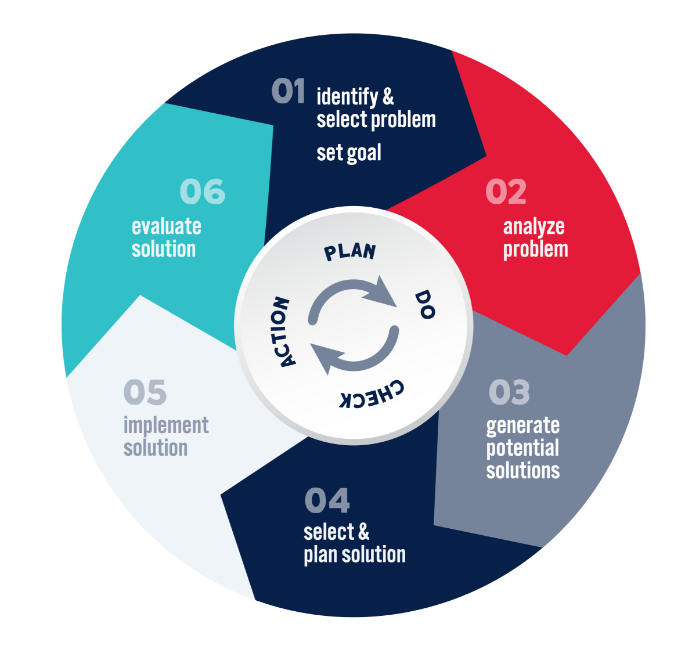
QUALITY
circles
Our company-wide quality circles are a key part of Dakkota and are used to improve morale and teamwork through team activity; increase self-development and communication; increase team problem-solving skills; and improve quality, safety, productivity, and the work environment.
We base our quality circle on the six steps in the Plan-Do-Check-Act (PDCA) cycle.
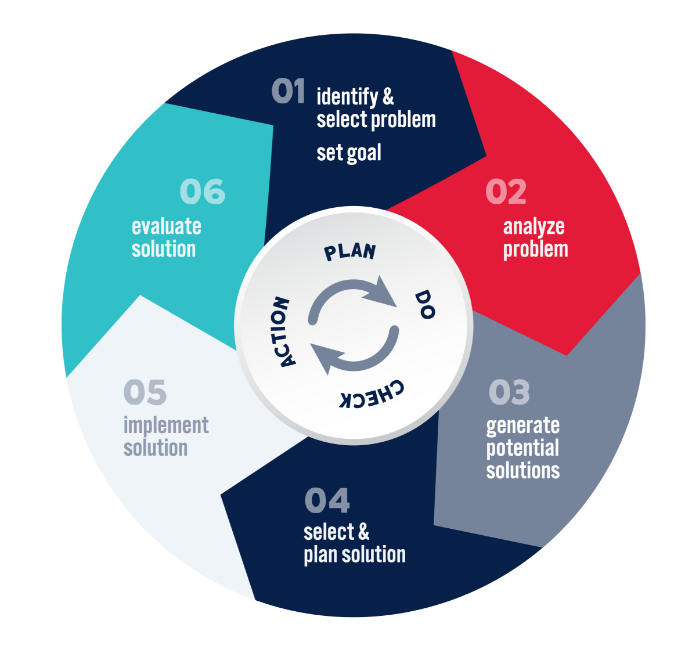
KETTERING PLANT
example
The Be the Change team worked to solve this issue: Team members needed to read build label for components required.
Solution: Look ahead pick screens installed to show critical part information to allow for prepick.
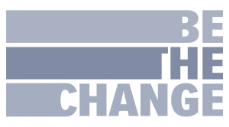
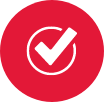
safety
Reduced walking and searching for parts
Reduced eye strain to read what parts required
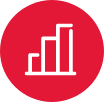
quality
Additional opportunity to inspect product for defects
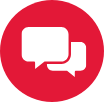
unity
Team members provided what data was most useful to display to optimize pick time
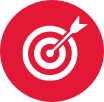
accuracy
Reduces opportunity to pick incorrect part
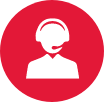
delivery
Reduced cycle time to pick by knowing exact parts required ahead of time
PROCESS
great ideas
The Great Ideas program has generated more than $36 million in savings from employee-generated ideas since it was formed in 2011. A bonus incentive for employees whose ingenuity results in an annual minimum of $1,000 or more in company savings, Great Ideas rewards group and individual ideas for process improvement in all areas. In addition to financial awards to team members, 25 percent of the savings created by the team is matched by the company and donated to a charity of the team’s choosing.
BE THE
change

Identify best practices and lean initiatives to improve our operations.

Develop project guidelines for each plant and extend positive change to other areas.

Develop Dakkota Change Champions from each plant to drive organizational changes throughout our footprint

Develop plant specific project plans with cross-functional teams.

Collaborate weekly, discuss best practices, and lessons learned.

Celebrate project success and sustain.
PROCESS
great ideas
The Great Ideas program has generated more than $36 million in savings from employee-generated ideas since it was formed in 2011. A bonus incentive for employees whose ingenuity results in an annual minimum of $1,000 or more in company savings, Great Ideas rewards group and individual ideas for process improvement in all areas. In addition to financial awards to team members, 25 percent of the savings created by the team is matched by the company and donated to a charity of the team’s choosing.
BE THE
change

Identify best practices and lean initiatives to improve our operations.

Develop project guidelines for each plant and extend positive change to other areas.

Develop Dakkota Change Champions from each plant to drive organizational changes throughout our footprint

Develop plant specific project plans with cross-functional teams.

Collaborate weekly, discuss best practices, and lessons learned.

Celebrate project success and sustain.